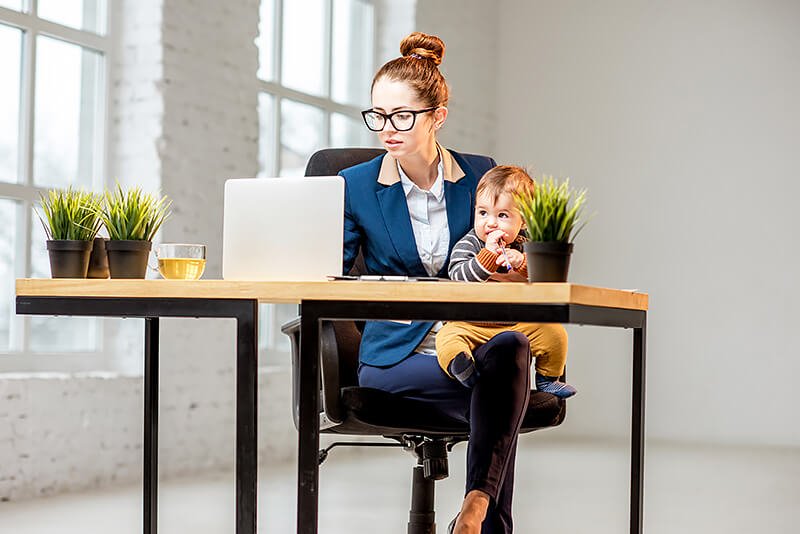
Extruder – Extrusion
In diesem Artikel möchte ich Ihnen ein bestimmtes Mechanisches Vorgehen näher bringen, welches Sie aus dem Bereich der Kautschuktechnik kennen. Es handelt sich hier um das Verfahren der Extrusion.
Um die Begriffe besser zu verstehen, erkläre ich Ihnen zunächst, was Extruder überhaupt sind. Es sind Maschinen oder auch Fördergeräte, die hergestellt wurden, um dickflüssige Massen unter einem sehr hohen Druck gleichmäßig aus einer Form zu pressen.
Sie kennen diesen Vorgang bereits als Kind, wenn Sie z.B. mit Knete bestimmte Muster aus einer Form gepresst haben, um es für Sie ganz simpel zu erklären. Der Unterschied hierbei ist, dass dieser Vorgang in der Chemie durch eine einfache oder auch doppelte Schraube ausgeführt wird. Quasi eine riesige Schraube, die das gewünschte Material ( z.B. Kunststoff ) durch die Öffnung oder auch Düse presst.
Diesen Vorgang kennen Sie auch als Extrusion. Stellen Sie sich den Aufbau dieser Maschinen wie folgt vor:Die horizontale Schraube, auch Schnecke genannt, ist links beginnend im Antrieb gelagert. Dieser wird durch einen Elektromotor angetrieben und sorgt für die Rotation der Schnecke. Rechts endet diese mit der Düse. Verbunden wird die Schnecke unterhalb mit einer Metallstange. Oberhalb des Extruders ist links außen ein Trichter angebracht, durch diesen dann das Material gegeben wird. Das ausgepresste Material wird auch als Extrudat bezeichnet.
Hierbei ist wichtig, dass nur ein bestimmtes Volumen an Masse in den Trichter gefüllt wird. Ummantelt ist die Schraube mit einem Zylinder. Rings um den Zylinder finden Sie versetzt ober- und unterhalb Heizbänder sowie Temperatursensoren. Diese sorgen dafür, dass genügend Hitze produziert wird, um das gewünschte Material besser formen zu können. Die Sensoren schützen vor Temperaturüberhitzung. Soweit zum groben Aufbau des Extruders.
Den Vorgang hatte ich Ihnen bereits in einfacher Form dargelegt und nun möchte ich Ihnen dieses genauer Beschreiben. Der Vorgang der Extrusion umfasst vier Zonen:
- Einzugszone
- Kompressionszone
- Ausstoßzone
Jede dieser Zonen besitzen eine wichtige Funktion, die ich Ihnen im folgenden Erläutern möchte.
- Einzugszone
In dieser Zone beginnt der Vorgang, denn hier wird das Material als erstes eingeführt und geschmolzen.
- Kompressionszone
Im weiteren Verlauf wird nun das Material durch Druckerhöhung weiter zusammengepresst.
- Ausstoßzone
Zum Schluss wird das Material zu einer geschmeidigen Masse verarbeitet, damit es besser durch die Düse ausgestoßen wird. Wie ich bereits erwähnte, sorgen Heizbänder für die Verflüssigung des Materials, um es besser zu verarbeiten.
Hierbei ist es aber auch möglich, dass bestimmtes Material (Wasser) gekühlt werden muss, u.a.auch durch Kühlkanäle, die ebenfalls im Schneckenzylinder zu finden sind. Je nach Materialverarbeitung wird der Aufbau durch zusätzliche Maschinen ergänzt.
Hierzu gehören u.a.auch Pumpsysteme die Gase aus dem Wasser pumpen, um Luftbläschen zu vermeiden. In den meisten Anlagen finden Sie einen komplexeren Maschinenaufbau, wie kühlende Wasserbäder. Doch auch der Schneckenaufbau ist unterschiedlich, je nach Materialverarbeitung. Dabei spielen u.a. die Scheckgenwindungen sowie der Abstand dazwischen und die Steigung eine wesentliche Rolle zum Verarbeiten der verschiedensten Materialien.
Daher gibt es auch verschiedene Arten von Extruder. Neben den Einschneckenextruder finden Sie außerdem noch die Gleichläufigen und Gegenläufigen Doppelschneckenextruder.
Zudem gibt es Vielwellen-, Kaskaden -, und Planetwalzenextruder. Lassen Sie mich kurz erläutern, wie diese verschiedenen Arten zu verstehen sind:
- Einschneckenextruder
Dieser Extruder umfassen einen Durchmesser von ca. 20 mm bis max. 400 mm und diese sind für sämtliche Kunststoffmaterialien geeignet. Das zu verarbeitende Material ist fein-rieselndes Granulat und eignet sich sehr gut, um in den Trichter eingefüllt zu werden.
Das Material wird nun durch einen sehr hohen Druck ( bis zu 500 bar ) geschmolzen und zur Masse verarbeitet. Da die Umdrehungen der Schnecke nur maximal 500 pro Minute schaffen, müssen zusätzliche Kräfte unterhalb der Achse geschaffen werden.
Wie bereits schon erwähnt, sorgen hier auch die Heizbänder für unterschiedliche Heiz-, aber auch Kühlprozesse. So sorgt ein Kühlgebläse für die Abführung der Energie des Extruder Zylinders.
Der Zylinder wird bis auf 280 Grad hoch geheizt und dehnt sich ca.3 Millimeter pro Minute aus. Die Maschine steuert die Regelung der Temperaturen und die Zahl der Umdrehungen.
Wie auch bei den anderen Extruder-Arten, wird das Material aufgeschmolzen und verarbeitet. Dies geschieht ebenso in drei Zonen, die ich Ihnen oben bereits erläutert habe.
In der Einzugszone wird der Feststoff konstant aufgeschmolzen. Dadurch wird das Volumen verringert, um den Druck aufzubauen und eine homogene Masse des Materials zu erzeugen.
- Gegenläufiger Doppelschneckenextruder
Dieser Extruder wurde zur Entwicklungen von Kunststoffröhren für Abwassersysteme verwendet. Hierzu werden Pulvermaterialien verarbeitet und stetig weiterentwickelt. Die Doppelscheckenextruder haben viele Vorteile u.a.lässt sich das Material besser verarbeiten, die Abgase können besser abgeführt werden und es entsteht nur eine geringe Temperaturerhitzung. Die Maschinen entwickelten sich zuverlässig und leistungsfähiger und sind heute absolut unverzichtbar. Zudem sind sie besonders vielseitig und können u.a. Platten, Rohre und auch Folien in verschiedenen Spritzgussverfahren herstellen. Hierbei unterscheiden Sie zwischen zwei verschiedenen Bauformen: parallel und konisch
Die parallele Bauart zeichnet sich durch einen konstanten und gleichförmigen Aufbau der Schnecke aus. Bei der konischen Bauweise ist der Aufbau stetig variabel. Neben den einfachen konischen Aufbau müssen Sie hier noch zwischen den super- konischer und doppel- konischer Aufbau unterscheide. Hier verläuft die Schnecke ähnlich wie bei einer Kegelform. Diese Kegelform erhöht den Druck massiv, aber ist meist nicht ausreichend. Daher werden öfter einfache – konische Systeme verwendet. Da diese Abwendungen nur bei geringer Ausstoßung angewandt werden, spricht man hier von einem Co – Extruder. Nachdem ich Ihnen den Unterschied beider Extruder erläutert habe, möchte ich Ihnen nun noch die Merkmale der parallelen und konischen Bauart näher bringen.
- Parallele Bauart
Ein hohes Spektrum an Schneckendurchmesser sowie eine unterschiedliche Längengestaltung der Maschinen, aber auch ein Kostengünstigere Herstellung und ein hoher Ausstoß sowie preisgünstigere Schneckenzylinder zeichnen die konische Bauart aus.
- Konische Bauart
Die Verarbeitung von unterschiedlichen Materialien wie Pulver, Granulat oder auch Mahlgut sowie eine sehr kompakte Bauart mit einem hohen Energieverbrauch, aber dennoch einer größeren Einzugsfläche und ein größerer Achsenabstand gewährleisten viele Umdrehungen und damit schnellere Materialergebnisse. Zum dem können die Schnecken einfacher abmontiert werden. Lassen Sie mich Ihnen im weiteren Verlauf nun den gleichläufigen Doppelschneckenextuder erläutern.
- Gleichläufiger Doppelschneckenextruder
Dieser Extruder wird heute sehr oft verwendet überwiegend für Kunststoffaufbereitung, aber auch in der direkten Verarbeitung u.a.beim Spritzgussverfahren. Hier wird Energiesparend gearbeitet. In der Lebensmittel – und Kautschukindustrie wird dieser Extruder am häufigsten verwendet. Die gleichläufigen Doppelschnecken sind, wie der Name schon sagt, zwei parallel laufende Schnecken in einem Zylinder, die in einer Richtung und einem gleichbleibenden Winkel verlaufen.
Die Schnecken stehen so eng beieinander, dass sie sich gegenseitig abstreifen. Das Fördergut oder auch Material wird von der einen zur anderen Schnecke übertragen. Das hat zur Folge, dass das Material besser gemischt und verarbeitet werden kann. Alle Prozesse des Verfahrens befinden sich im Verfahrensteil. Dieses ist seit 1960 flexibel auf verschiedensten Verfahren anwendbar. Durch ein hohes Drehaufkommen verzahnen sich die Schnecken.
Durch ein bestimmtes Luftverfahren wird die Festigkeit erhöht. Der Durchmesser des Extruders bestimmt die Länge und den Zylinder der Schnecken. Auch hier finden Sie wesentliche Vorteile zum Einschneckenextruder, die ich Ihnen hiermit aufzeige. Durch die größere Einzugsöffnung kann das Material schneller befördert werden und dadurch verläuft der Prozess innerhalb kürzester Zeit. Außerdem sorgen die doppelten Schnecken für eine geschmeidigere Masse und reinigen sich besser. Auch der flexible Aufbau garantiert verschiedene Formen.
Nachdem ich Ihnen nun die unterschiedlichen Arten des Schneckenaufbaus geschildert habe, möchte ich Ihnen kurz noch die Werkstoffe vorstellen, die extrudiert werden. Das sind u.a. natürlich Gummi und Kautschuk, Ton- und Keramikmassen, zahlreiche Kunststoffarten wie PVC oder auch PP und PET.
Nicht zu vergessen sind in der Lebensmittelherstellung die Teig-förmige Lebensmittel und auch Futtermittel. Doch welche Extrusionsprodukte entstehen können, lesen Sie im weiteren Verlauf. Es entstehen u.a. Kunststoff und Pulverlack, Röhre und Stäbe, Fensterrahmen und Dichtungen, zahlreiche Kabelummantelungen und Schläuche, Türdichtungen sowie Wischgummi für Scheibenfischer sowie Rückspiegelfassungen und Innentürverkleidungen. Wie bereits erwähnt, schrieb ich von verschiedenen Verarbeitungen.
So ist z.B. durch einen Blaskopf und Breitschlitzdüse auch eine Folienproduktion möglich oder aber auch Platten, die durch erneutes erhitzen, verformbar sind. Sie sehen, dass die Bandbreite unglaublich groß ist und vielseitig.
Doch welches ist nun das Beste Verfahren?
Mein Fazit ist, dass ich, aufgrund der vielen positiven Vorteile, die gegenläufigen Doppelschneckenextruder durchgesetzt haben. Nicht nur durch die schnellere Verarbeitung und die geringe Belastung, sondern sie haben sich immer weiterentwickelt
When you’re a carpenter making a beautiful chest of drawers, you’re not going to use a piece of plywood on the back, even though it faces the wall and nobody will ever see it. You’ll know it’s there, so you’re going to use a beautiful piece of wood on the back.Steve Jobs
Neueste Kommentare